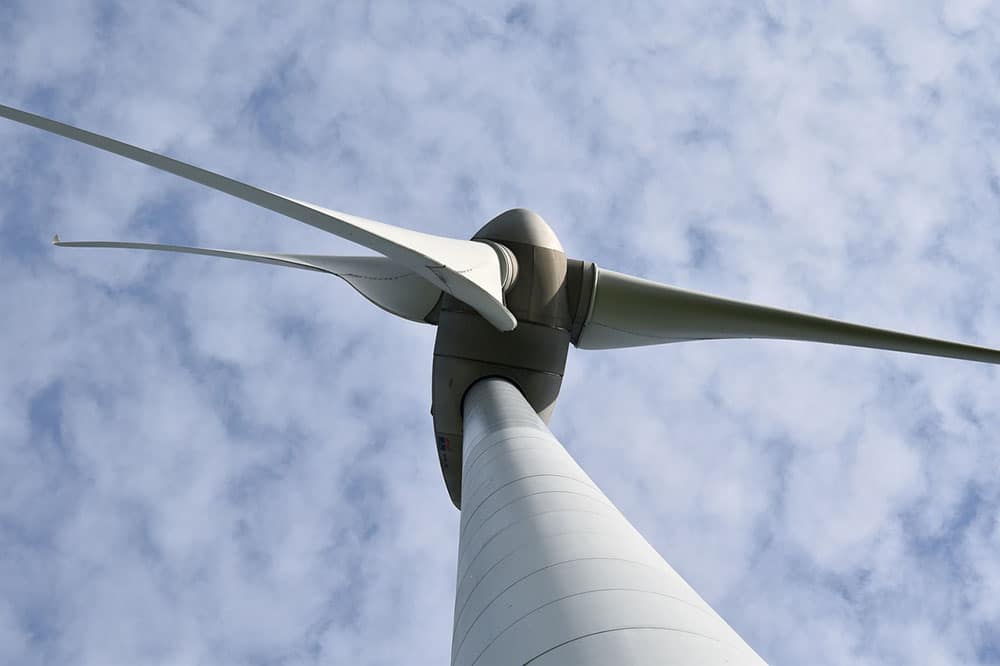
The Rise of Wind Energy
Wind energy isn’t a new concept. For thousands of years, people have harnessed the wind. Think of the simple sailboats that utilized wind for propulsion or the traditional windmills of Holland. But today’s wind energy landscape is vastly different, marked by technological marvels like the towering wind turbines we see dotting landscapes and off-shore expanses.
Over the past few decades, we’ve witnessed wind power’s meteoric rise. It’s clean, sustainable, and increasingly cost-effective. But what enables the conversion of simple wind into usable electricity? The answer lies in the design and interplay of the components of wind turbines.
Each wind turbine is a symphony of engineering, where every component, be it as visible as the blades or as hidden as the generators inside, plays a crucial role. Their objective? Capture the kinetic energy of wind, convert it to mechanical energy through rotation, and finally, transform it into electricity that powers our homes and businesses.
In the next sections, we’ll unpack blades, towers, generators, and more to find out what truly makes up a wind turbine.
Blades: The Wind Catchers
If you’ve ever seen a wind turbine in motion, the first thing you’d likely notice is its massive blades, sweeping through the air with grace despite their size. These blades aren’t just for show; they’re the frontline soldiers capturing the wind’s kinetic energy. Let’s dive into how they’re designed and why they work the way they do.
1. Design and Dynamics
Wind turbine blades are marvels of aerodynamic engineering. Taking cues from airplane wings, their shape is designed to maximize the lift while minimizing the drag. When wind flows over them, the pressure difference between the blade’s curved top surface and flatter bottom surface results in lift. This force turns the blades around the rotor hub.
Materials matter. Most blades are crafted from lightweight, durable materials such as fiberglass, reinforced plastics, or carbon fiber. These ensure the blades can withstand the force of strong winds while staying efficient.
2. Length and Rotation
You may wonder, why are some blades longer than others? Blade length impacts the amount of energy a turbine can capture. Longer blades sweep a larger area, thus harnessing more wind. However, they rotate at slower speeds. Conversely, shorter blades cover a smaller area but can rotate faster. The choice of blade length usually hinges on the specific goals of the wind project and the wind speeds of the location.
3. Angle and Adjustments
Blades aren’t static; they can adjust their angles based on wind speed. This ability to “pitch” helps in optimizing energy capture and protecting the turbine during very high winds. When the wind’s too strong, blades pitch out of the wind to reduce their rotational speed. Conversely, in lighter winds, they might align more directly with the airflow to maximize rotation.
4. Wear and Tear
Like all moving parts, blades experience wear. Erosion, especially at the tips where they move the fastest, can affect performance. Regular maintenance checks ensure they remain in top shape, maximizing energy capture and prolonging the turbine’s life.
Blades aren’t just static arms protruding from a turbine; they’re dynamic and adaptable components crucial for harnessing wind energy. Every design choice, from length and material to adjustability, serves the purpose of maximizing energy generation from the wind. The blades set the pace, and the rest of the turbine components follow suit, channeling, and converting this captured energy. In the next section, we’ll see how the tower, an often overlooked component, plays a crucial role in a wind turbine’s effectiveness.
Towers: The Pillars of Wind Power
At a glance, the tower of a wind turbine might appear to be a simple metal column, a structure that merely supports the dynamic components above. However, the tower’s role in the efficiency wind energy capture are crucial.
1. Height Matters
One of the core principles behind tower design is the concept that wind speeds increase with altitude. Higher altitudes usually equate to more consistent and stronger winds. Thus, taller towers can access faster wind speeds, translating to more energy. By elevating the blades and nacelle (where the generator is housed), towers ensure that turbines catch the most potent part of the wind.
2. Structural Integrity
Given their stature, towers must withstand not only the weight of the turbine components but also the dynamic forces of the rotating blades and the pressure of fluctuating winds. Constructed primarily from tubular steel, concrete, or even a combination of both, towers have a tapered design. This ensures that the maximum strength and stability are concentrated at the base, where the greatest stress occurs.
3. Types of Towers
Tubular Steel Towers: These are the most common and are characterized by their sleek, cylindrical shape. They’re pieced together using sections for ease of transport.
Lattice Towers: Recognizable by their open framework, lattice towers were more common in older wind farms. Though they use less material, they’ve largely been replaced by tubular designs due to aesthetic and maintenance preferences.
Concrete Towers: Rising in popularity, especially for taller structures, these towers often employ a hybrid design, combining concrete bases with steel tops. The added mass provides enhanced stability.
4. The Foundation’s Role
Anchoring these massive structures is a foundation, often buried several meters into the ground. Depending on the site’s soil and rock conditions, the foundation might be a massive concrete slab or a network of deep-set pilings. It’s designed to distribute the load evenly and ensure the turbine remains upright even during the most extreme weather events.
5. Maintenance and Lifespan
Towers, like all parts of a wind turbine, have a lifespan. Over time, they can suffer from corrosion, especially at their base, where moisture and environmental conditions can be most aggressive. Regular inspections are vital, searching for signs of stress, rust, or structural issues. Protective coatings and cathodic protection systems can prolong their life.
The tower isn’t merely a stand for the turbine’s moving parts. It’s a critical component, thoughtfully designed to elevate the turbine to optimal heights, withstand immense forces, and serve as the steadfast backbone of the entire system. As we move to the next section, we’ll delve into the heart of the turbine: the generator, where captured wind energy gets transformed into electricity.
Generators: The Heart of Wind Turbines
If towers serve as the backbone of a wind turbine, the generator is its beating heart. As wind drives the turbine’s blades, this captured kinetic energy needs conversion into something we can use: electricity. That’s precisely the role of the generator.
1. The Basic Mechanism
The generator works on a simple principle: electromagnetic induction. Inside the generator, there’s a tight interplay between moving magnetic fields and stationary electrical conductors. As the rotor, driven by the blades, turns within the generator, it causes a magnetic field to move relative to these conductors. This movement induces a flow of electricity.
2. Types of Generators Used in Wind Turbines
Synchronous Generators: These generators run at the same speed as the grid frequency. They can operate at constant speed or variable speed. For variable speed, these machines often require complex electronics.
Asynchronous (or Induction) Generators: More common in wind turbines, they can operate at a variety of speeds. These generators are self-exciting, meaning they draw reactive power from the grid to initiate electricity generation.
3. Direct Drive vs. Gearbox Systems
The debate between direct drive and gearbox systems is a noteworthy one in the world of wind turbines.
Direct Drive: As the name suggests, the rotor is connected directly to the generator, without a gearbox. This means fewer moving parts, which could mean less maintenance. However, these systems typically require larger and more costly generators.
Gearbox Systems: These systems employ a gearbox to increase the rotational speed from the rotor to the generator. While it introduces more components (and potential failure points), gearboxes allow for the use of smaller, more economical generators.
4. Cooling Systems: Keeping Things Operational
Generators produce heat, and if left unchecked, this heat can degrade components and reduce the lifespan of the generator. Wind turbine generators often incorporate either air or liquid cooling systems to maintain temperatures. The choice between the two often depends on the turbine’s size and its operating environment.
5. The Push for Innovation
As the demand for wind energy grows, so does the push for more efficient and reliable generators. Advances in superconducting materials offer the potential for smaller, more potent generators. Additionally, innovations in electronics and control systems allow for smarter, more adaptable operations, adjusting to fluctuations in wind speed and direction for optimal power generation.
In essence, the generator is where the magic happens, where the swirling, powerful gusts of wind get transformed into clean, usable electricity. While the principles of electromagnetic induction remain consistent, the quest for improved designs and materials never ceases.
The Nacelle: Housing Critical Components
The nacelle of a wind turbine might be likened to the cockpit of an aircraft. Positioned atop the tower and directly behind the rotor, this vital enclosure protects the heart of the turbine’s operational systems.
1. Construction
Constructed from robust materials, often composites or metals, the nacelle is designed to endure extreme weather conditions. This sturdy structure shields internal components from rain, snow, and intense wind, ensuring longevity and consistent performance.
2. Internal Components
Within the nacelle, a myriad of essential equipment finds its home:
- Controller: This device determines the start and shutdown of the turbine based on wind speeds. It helps protect the turbine from potentially damaging high-speed winds.
- Braking System: Safety is paramount. If wind speeds become too high, or in case of a malfunction, the braking system can halt the turbine’s rotation to prevent damage.
- Gearbox: While we touched on this in the generators section, it’s worth noting that in turbines with a gearbox, it’s housed in the nacelle. It’s here that the rotation speed amplifies before transferring to the generator.
- Yaw Drive and Yaw Motor: Wind direction isn’t constant. The yaw drive and yaw motor enable the turbine to rotate and face the wind directly, optimizing energy capture.
3. Maintenance Access
Given the plethora of critical components within, the nacelle often features access points for maintenance personnel. Whether it’s regular check-ups, component replacements, or system upgrades, easy accessibility is crucial.
4. Cooling and Ventilation Systems
Beyond just the generator, several components within the nacelle produce heat during operation. To ensure these parts operate efficiently and don’t overheat, cooling and ventilation systems are integrated into the nacelle’s design. These systems help maintain an optimal internal temperature, regardless of the external climate.
5. Improvements
As with other parts of the wind turbine, the design and functionality of nacelles have seen significant advancements over the years. Modern nacelles are becoming more aerodynamic, reducing drag and thus increasing overall efficiency. Additionally, innovations in material science have led to lighter, yet more durable nacelles, able to withstand the harshest environmental conditions.
Foundations and Support Structures
Every structure relies on strong foundations. In the context of wind turbines, while blades, towers, and nacelles steal the spotlight, it’s the foundations and support structures that root them firmly to the ground.
1. Types of Foundations
Different terrains and environments call for varied foundation designs. Let’s break down the most common ones:
- Gravity Foundations: These are heavy concrete slabs that simply use sheer weight to anchor the turbine. They’re often used in onshore wind farms because of their simplicity and effectiveness.
- Pile Foundations: Driven deep into the ground, pile foundations are like giant stakes that keep the turbine stable. They’re especially useful in places with soft soil, ensuring that the turbine stays upright even in challenging conditions.
- Floating Foundations: As offshore wind farms become increasingly prevalent, floating foundations are gaining traction. Anchored to the seabed using mooring lines, they allow turbines to be deployed in deep waters.
2. Integration with Towers
Foundations are never isolated components. They’re intricately linked to the turbine towers, transferring loads and stresses efficiently. Special connectors, often made of steel, are used to join the tower to the foundation, ensuring a stable and unified structure.
Yaw and Pitch Systems
The yaw and pitch systems adjust the turbine’s orientation and blade angles, respectively, to ensure efficient operation regardless of how the wind blows.
1. What is the Yaw System?
The yaw system rotates the nacelle (and thus the blades) to face the wind directly. It’s essential because direct wind capture is vital for optimal energy generation. Here’s a closer look:
- Yaw Drive and Motors: These components are responsible for the actual turning of the nacelle. Working in tandem, they ensure the turbine aligns with wind direction.
- Wind Direction Sensors: Typically located on top of the nacelle, these sensors feed real-time data to the turbine’s control system, prompting the yaw drive to act when wind direction changes.
- Yaw Brakes: These prevent the nacelle from over-rotating or spinning uncontrollably, a safety mechanism to protect the turbine and its components.
2. Pitch Systems: Fine-Tuning Blade Angles
The pitch system adjusts the angle of the turbine blades. By altering the blade pitch, turbines can capture wind energy efficiently, irrespective of wind speed. Key components include:
- Pitch Control Mechanism: Using hydraulics or electromechanical actuators, this mechanism alters the blade’s angle concerning the wind.
- Wind Speed Sensors: These devices measure wind velocity, enabling the control system to decide the best blade angle for given conditions.
- Safety Systems: In extreme winds, the pitch system can adjust the blades to a ‘feathered’ position, minimizing drag and preventing potential damage.
Wind Turbines for Home Use
There are wind turbines designed specifically for home use. These residential wind turbines are generally smaller than commercial ones, and they can be mounted on rooftops or on standalone towers. Their power output varies depending on their size and the wind conditions in the area.
Smaller wind turbines might only produce enough energy to charge batteries or power small appliances. However, larger residential turbines can generate a significant portion of a home’s energy needs, and in some cases, might even produce surplus electricity that can be sold back to the grid.
It’s crucial to note that wind turbines for home use require careful planning and consideration. Factors such as the local wind conditions, the size of the turbine, zoning regulations, and potential impacts on neighbors and wildlife all need to be taken into account. Additionally, residential wind turbines are usually more cost-effective when used in combination with other renewable energy sources and energy efficiency measures.
While it’s true that a single small wind turbine might not be able to power an entire house on its own, it can still contribute to a home’s energy needs and help reduce reliance on the grid. This can be especially beneficial for those living off-grid or seeking to adopt a more sustainable lifestyle.